We often think of water as being essential to life, but it can be very detrimental in manufacturing. In an air compressor set up, water vapor becomes concentrated during the process of air compression. If allowed to build up, this excessive water can lead to a variety of operational problems and production complications.
An industrial compressed air dryer is used to separate water vapor from process air and cool it, so the air can be compressed efficiently. This step is necessary to prevent such production failures as freezing outdoor air lines, dangerous corrosion in piping and equipment, and malfunctioning of pneumatic process control instruments.
GEM distributes a variety of compressed air dryers to keep production running smoothly.
Our line includes regenerative, breathing air system, membrane, and refrigerated cycling and non-cycling. Air dryers are essential to keep your air compressor set up free of moisture, and prevent rust build-up. This article looks at the different types of compressed air dryers, and discusses some possible applications for each.
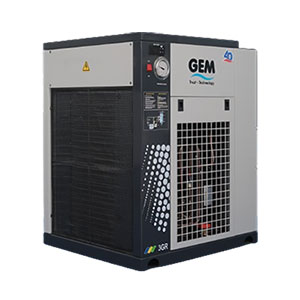
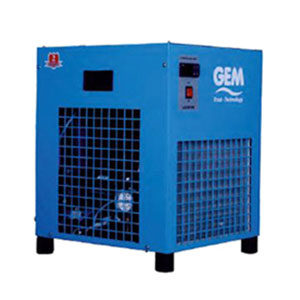
Refrigerated Air Dryers
Refrigerated air dryers are typically used in industrial applications because they are easy to maintain, relatively low-cost, and have few special requirements. Similar to a home refrigerator or air-conditioner, the industrial refrigerated air dryer works in the following way:
- Warm, moist air enters the air dryer.
- It is rapidly cooled to a temperature slightly above freezing in a refrigeration unit.
- The water vapor condenses into liquid water.
- The water is collected in a trap and emitted through discharge lines.
- The warm, gaseous refrigerant is cooled and regenerated in a condenser.
- The remaining dry air is then reheated to room temperature and fed through an outlet.
Refrigerated air dryers are typically best used for general plant operations, as opposed to critical processes that may require extremely dry air.
Desiccant-Type Air Dryers
In these dryers a desiccant is used to adsorb water vapor in the air stream. Here the moisture adheres to the desiccant itself, and collects in the pores of the desiccant beads. Because they are capable of achieving a very low dew point, these dryers are perfect for use in colder climates or for industries which require super dry air.
Although a single tower set-up is possible, desiccant-type air dryers usually have a twin tower construction. One tower is used to dry the air, while spent desiccant is regenerated in the second tower. Moisture is driven off by a dry air purge, heat, or some combination of both.
The dry air process utilizes purge air to expel moisture, which can fall in a range of up to 18% of the total air flow. The dew point rating in the desiccant dryer is about -40°F, but it can be driven as low as -100°F. The heated process has a heater in the circuit, with similar dew points. Valves are used to divert about 8% of the air which is leaving the drying tower and send it through the heater. The hot and dry air is then passed through the regenerating tower, with captured moisture discharged to the outside.
Cost is an important deciding factor in choosing a desiccant-type air dryer. A heated dryer may use about half of the compressed air for regeneration, but they do require a lot of electricity. On the other hand, the heatless dryer offers great energy savings. With these dryers, you also need to remember the cost to periodically replace the desiccant bed, usually every 3-5 years.
Major Locations in Tamil Nadu
We proudly serve various industrial hubs across Tamil Nadu, offering high-quality cooling tower solutions tailored to the needs of each region. Our presence spans the following key cities:
Cooling Tower Manufacturer in Chennai
Cooling Tower Manufacturer in Coimbatore
Cooling Tower Manufacturer in Madurai
Cooling Tower Manufacturer in Tiruppur
Cooling Tower Manufacturer in Trichy
Cooling Tower Manufacturer in Erode
Cooling Tower Manufacturer in Salem
Cooling Tower Manufacturer in Vellore
Cooling Tower Manufacturer in Thoothukudi
Cooling Tower Manufacturer in Nagercoil