Air driers are installed to remove the remaining moisture from the compressed air. Basically, two types of air driers are in common use today viz., Refrigerated driers and Regenerative driers.
Using a principle similar to that of the cycling-type driers, on some designs the thermal mass takes the form of an Intermediate circuit or water loop containing water or a glycol solution. The cold liquid refrigerant passes through a heat exchanger, cooling the fluid in the water loop, which, in turn, passes through another heat exchanger to cool the air. The use of the water loop modulates temperature fluctuations, preventing the freezing of condensate in the air circuit. This design is generally limited to larger driers (approximately 5000 scfm - 8500 scfh) and larger and nominally rated for 50°F (10°C) pressure dew point performance.
Most refrigerated driers also incorporate an air-to-air heat exchanger, which serves two purposes:
(1) hot incoming air is precooled by the cold outgoing air, which reduces the load on the refrigeration system; thus allows the use of a smaller refrigeration condensing unit and reducing energy requirements.
(2) Outgoing cold air is warmed, preventing condensation or sweating on the outside of the air Iines down-stream.
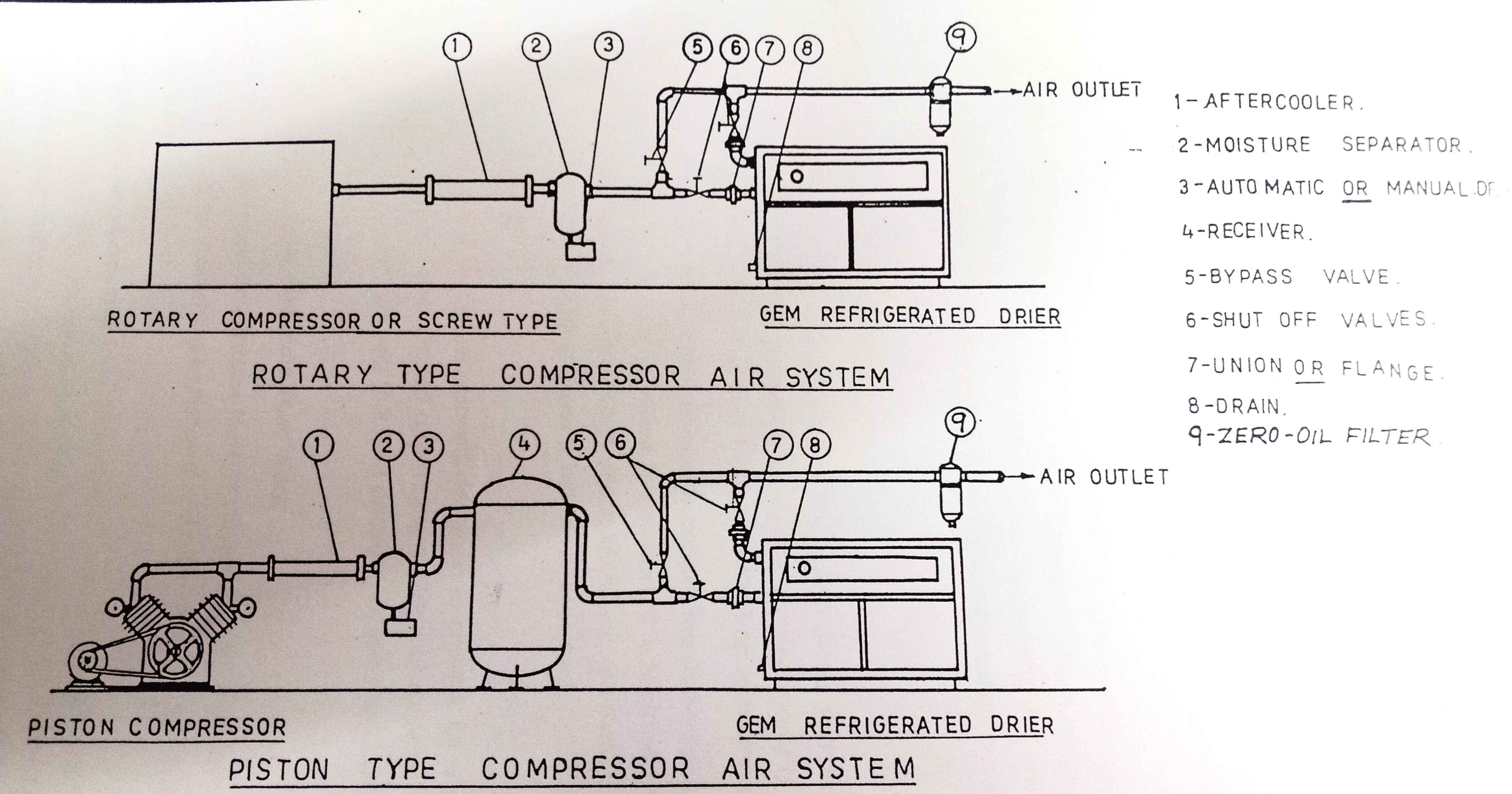
Adsorptive Desiccant Drier
- Adsorptive desiccant driers absorb moisture from compressed air as the compressed air passes through the desiccant. Adsorption is a physical process of condensing and holding moisture on the surface of a porous area of a hygroscopic or moisture-attracting substance.
Hygroscopic materials are solid substances that have the ability to attract moisture. These driers may use a single tower of desiccant where the desiccant Is replaced when saturated, however, they normally consist of two towers through which airflow is alternated so that one tower is drying the compressed air while the other tower is being regenerated.
Degree Of Drying
- Adsorptive desiccant driers are normally designed to provide air at 40°F (-40°C) pressure dew point. Lower dew points can be supplied depending on the type of desiccant and dryer design, reaching as low as -100°F (-73°C) at 100 psig (6.9 bar) pressure, or less than I part per million of water vapor (by volume).
Adsorptive Desiccants and How They Work
Silica gel is a granular, amorphous form of silica made from sodium silicate and sulfuric acid. It has a high capacity for adsorbing water and Is readily reactivated by heating or purging with dry air or a combination of both.
Activated alumina is a porous form of aluminum oxide with a high surface or pore area. For compressed- air drying, a type that combines aluminum oxide and some silicon dioxide is generally used. This is in the form of small balls and is highly resistant to shock or contact with liquid water. It is readily reactivated by heating by heating or purging with dry air or a combination of both.
Refridgerated Driers
- Refrigerated driers remove moisture from compressed air by cooling the air in an evaporator, thereby reducing the ability of the air to hold moisture. The cooling effect is derived from the evaporation of a liquid refrigerant. The resulting moisture condensed out of the air is then removed by a separator and trap.
Refrigerated driers are generally rated for pressure dew points of 33° to 39°F (0.56° to 3.9°C), as rated by ANSI B93.45M-1982 under the following conditions: pressure, 100 psig (6.9 bars); Inlet air temperature, 100°F (37.8°C), ambient air temperature, 100°F (37.8°C); pressure drop, not greater than 5 pslg (0.35 bar). This is specified by the manufacturers nominally as 35°F (1.67°C), though some large-capacity units are nominally rated for 50°F (10°C). As long as the compressed air leaving the refrigerated drier is not exposed to temperatures below its pressure dew point, there will be no further conditions in the downstream system.
The principle used in a refrigerated air dyer is essentially the same as that used in an ordinary refrigerator air conditioner. In a direct-expansion dryer, the simplest and most common type, high-pressure liquid refrigerant, typically a fluorinated hydrocarbon, is supplied to the evaporator from the condenser by the refrigerant compressor. The high pressure of the liquid Is metered into the evaporator using any one of various control devices. The function of the control device is to pass liquid refrigerant into the evaporator and to lower the pressure of the liquid. This reduction in pressure causes the liquid to boil until the refrigerant is at its saturation temperature corresponding to its pressure.
As the low-pressure refrigerant passes through the evaporator, heat flows from the compressed air into the refrigerant, causing the boiling to continue until the refrigerant is completely vapourised. This process cools the air, reducing its capacity, to hold water vapor. The excess vapor condenses to a liquid and is removed from the air stream by a separator and drained from the system.
The refrigerant vapor leaves the evaporator and travels to the refrigerant compressor, which compresses it to a hot, high-pressure gas. This gas is forced into a condenser where it is cooled, either by water or forced ambient air. When the refrigerant vapor reaches its saturation temperature, it condenses into a high-pressure liquid. This liquid is returned to the evaporator, and the cycle is repeated. Non-cycling, direct-expansion driers use a capillary tube system of a thermostatic expansion valve in conjunction with a hot gas bypass valve to regulate the flow of refrigerant to the evaporator to compensate for load fluctuations and to prevent freezing under no-load or low-load conditions. Cycling driers use a thermal mass surrounding the air passage in the evaporator. This mass may be a liquid. usually glycol or a related substance, or a metal, such as aluminum block, beads, or particles. Under reduced load conditions the thermal mass previously chilled by the refrigeration system tends to stay cold, allowing the refrigeration compressor to be shut off. As the thermal mass warms up, a thermostat restarts the compressor. This allows the compressor to cycle on and off rather than run continuously, as in a noncycling-type dryer. Molecular sieves are crystalline metallic aluminum silicates that belong to the class of compounds called zealots. The sieves are available in various pore sizes, which are used for the adsorption of selective gases and vapors. They may be In the form of small spheres or cylindical extrusions. Reactivation is accomplished by heating or purging with dry air or a combination of both.
Adsorptive Desiccant Drier Equipment
- The simplest form of adsorptive desiccant dryer is a single-bed vessel containing desiccant. As the compressed air flows through the dryer, the desiccant becomes saturated. At this point, the desiccant must be removed and replaced with a new, dry desiccant, or the old desiccant can be reused after regeneration by heating with a new, dry desiccant, or the old desiccant can be reused after regeneration by heating in an oven. The single-tower desiccant dryer is usually limited to applications requiring a very small airflow or periodic usage.
For most application, desiccant driers generally employ dual towers. There are two basic types: beat- reactivated driers and heatless-type driers.
Heatless driers are purge-type driers without heaters. They rely on frequent air flow reversals through the towers, which allow only a small amount of moisture to be adsorbed by the desiccant. After the short adsorption period, there is a rapid depressurization, which lowers the partial pressure of the water vapor so that it is desorbed from the desiccant and purged from the tower by a relatively high volume of dry process air. Although the heat of adsorption is utilized to aid reactivation, an amount of dry purge of approximately 15 to 20 percent of the inlet air stream is required. These driers normally operate on a 10-minute cycle (5-minute adsorption, 5-minute reactivation). Often, shorter cycles or different desiccants are used to produce lower effluent dew point performance. Because of the high loss of compressed required for regeneration, these driers are more popular In the smaller-capacity range, 1 to 100 scfm (1.7 to 170 cmh). These driers have an advantage when installed In remote locations where no electric power is available since the driers can be designed for a completely-air system.
Specifying a Compressed Air Dryer
- The air dryer with certain auxiliary equipment becomes a system that is an important component of the whole plant compressed-air system. Various components comprising the dryer subsystem should be selected on the basis of the overall requirements and the relationship of the components to each other. In addition to the required compressed-air flow, there are just three main factors to determine in selecting the appropriate dryer to provide the required performance: dew point, operating pressure, and inlet temperature.
Dew Point
- Dew point performance from regenerative desiccant driers is nominal -40°F (-40°C) or lower at operating pressure and 100°F (38°C) saturated inlet air.
Refrigerated driers provide nominal dew points of 35° or 50°F (2° or 10°C) at operating pressure based on saturated Inlet air at 100°F (38°C).
Deliquescent driers are more sensitive to the inlet temperature and are based on saturated inlet air at 100°F (38°C), provide a dew point from 65° to 80°F (18° to 27°C) at operating pressure.
Operating Pressure
- At higher pressures, saturated air holds less moisture per standard cubic foot than at lower pressures.
Considering air at 100 psig (6.9 bars) as the normal pressure, the moisture-holding potential increases rapidly at lower pressures. At higher pressures, above 100 psig (6.9 bars), the potential water content increases at a much slower rate as the pressure rises. Drying air at the highest pressure consistent with the air system design will result in the most economical operation.
Inlet Temperature
- The temperature of air entering the dryer is usually close to the temperature at which it leaves the aftercooler. Saturated air at 100°F (38°C) contains almost twice as much moisture as saturated air at 80°F (27°C).
For every 20°F (11°C) increase in the temperature of saturated air, there is an approximate doubling of the moisture content. Thus it is desirable to operate the dryer at the lowest feasible temperature.